Motion Supervisor Object 
Motion Supervisors can be thought of as specialized
task-masters for motion control. Many system designers find it convenient
to divide their system into specialized sub-tasks, each handled by a separate
motion supervisor. As you organize your motion control system, the advantages
of this approach will become obvious.
The Motion Supervisor summary window is divided into
two configuration tab pages, plus a General Status page as shown below,
and includes such attributes as Motion Type and Stop Time:
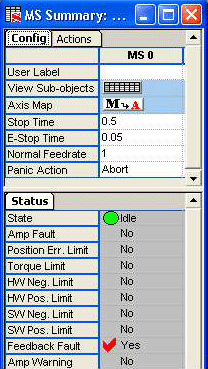
User Label – User-defined label for the object.
View Sub-objects – Shows all sub-objects for
the Motion Supervisor. For more information, see Object
Summary Windows.
Axis Map – Displays the MS Axis List Configuration
window. For more information, see the Object List
Configuration Dialog Boxes section.
Stop Time –Time (in seconds) to decelerate axis
to a stop.

CAUTION! Actual stopping time is limited
by mass and speed! If you are moving a heavy object at high speed and
command a very rapid Stop Time, your motion control or mechanical system
may be unable to comply. Verify that drive and motor manufacturer's specifications
meet the demands placed upon your system BEFORE assuming a stop time.
E-Stop Time – Time to decelerate to an emergency
stop. When E-Stop is activated, the State will be flagged with a Stopping
Error while the axis is decellerated. An Error state is flagged when the
axis comes to a complete stop. However, amp enable outputs are NOT disabled.
NOTE: If the axis is close to completing a move when E-Stop is activated,
the axis may halt before the E-Stop Time has expired.
Normal Feedrate – Speed scaling factor applied
to movement. 0 = stopped; 1 = normal speed (unscaled); 1.5 = 150%; 2 =
200%, -1 = reversed norma speed; etc.
Panic Action – Action to execute when the
panic key is activated.
NOTE: Some panic action states (E-Stop and Abort) flag a fault condition.
To reset the system after a fault, click on the Clear Fault button (MS
Summary / Actions tab page).
- None – Motion is halted at the end of the currently
commanded move. (No-fault condition.)
- Stop – Motion is halted using a Stop. (No-fault condition.)
- E-Stop – Motion is halted using an E-Stop, and a fault
condition is flagged.
- E-Stop, Abort – Motion is halted using both an E-Stop
and an Abort, and a fault condition is flagged. A fault condition
is flagged.
- Abort – Motion is halted using an Abort.
|
Configuration Attributes: "Actions" Tab Page
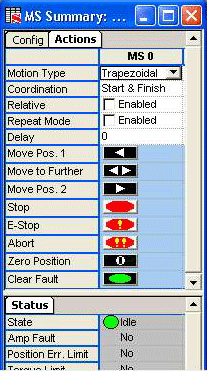
Motion Type – The motion type specifies the profile for the commanded motion trajectory.
- Trapezoidal – Implements a trapezoidal velocity trajectory to reach the target position. Does not use the Jerk Percent parameter.
- Cartesian Trapezoidal – For multiple axes per MS. Implements a trapezoidal velocity trajectory with each axis’ component velocity, acceleration, and deceleration scaled by the ratio of the axis move distances. The first axis’ motion parameters specify the vector velocity, vector acceleration, and vector deceleration for the resultant vector profile.
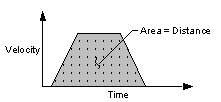
- S-Curve Jerk % – Implements an S-curve velocity trajectory, using the Jerk Percent parameter to reach the target position.
- Cartesian S-Curve Jerk % – For multiple axes per MS. Implements a trapezoidal velocity trajectory with each axis’ component velocity, acceleration, and deceleration scaled by the ratio of the axis move distances. The first axis’ motion parameters specify the vector velocity, vector acceleration, and vector deceleration for the resultant vector profile.

Coordination – Determines the coordinated behavior when 2 or more axes are mapped to a motion supervisor:
Start – Axes start at the same time and each axis uses its specified motion trajectory parameters. Axes may finish at different times, depending on their specified trajectory parameters.
Finish - Axes finish at the same time and each axis uses its specified motion trajectory parameters. Axes may start at different time, depending on their specified trajectory parameters.
Start and Finish – Axes will start and finish at the same time. The trajectory parameters are scaled lowered based on the axis whose trajectory profile takes the longest time.
Delay – Time delay (in seconds) before execution of next move command. If operating in Repeat Mode, the delay will be applied to the beginning of each move segment.
Repeat Mode – [Enabled; (not enabled)] Repeats
programmed motion.
NOTE: Each repeated motion will be delayed by the Delay amount (see
description above on Delay).

Move Pos. 1 – Command each axis associated with the Motion Supervisor
to Position 1.

Move to Further – Command each axis associated with the Motion Supervisor
to either Position 1 or Position 2, whichever is further away.

Move Pos. 2 – Command each axis associated with the Motion Supervisor
to Position 2.

Stop – Stops movement of objects under control of current Motion
Supervisor within Stop time (seconds).

E-Stop – Emergency stop. Halts movement of objects under control
of current Motion Supervisor within E-Stop time (seconds) and leaves the
axes in an Error state.
NOTE: E-Stop does NOT disable closed-loop control and does not disable
the amp enable output(s).

Abort – Immediately stops movement of objects under control of current
Motion Supervisor, disables closed-loop control, and disables the amp
enable output(s), leaving the axes in an Error state.

CAUTION! Do not
use Abort when testing equipment which depends upon servos or stepper
motors to secure personnel or equipment (e.g., lifting cranes, elevators,
etc.). The Abort command disables servos and steppers and, in some circumstances,
may present a hazard to personnel or equipment due to sudden loss of power.

Zero Position – Sets the origin of the axis to the current actual
position and the command position to 0. The algorithm for setting the
origin is: new origin = current origin + actual position

Clear Fault – Clears the Motion Supervisor's error state and all
sub-object statuses. If you are having problems clearing the faults, it may be a result of improper axis mapping. Please see the Troubleshooting section.
Status Attributes
Status fields are read-only:
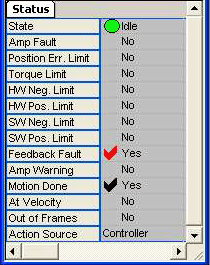
Motion States
State – Current motion state. See Motion States
table below.
Motion States
Error States
 |
A black checkmark indicates something positive.
(ex: Motion Done, At Target) |
 |
A red checkmark indicates something potentially negative.
(ex: error states, limits, amp fault, etc.) |
Error |
Flag |
Description |
Amp[lifier] Fault |
|
Yes - Amplifier fault. |
Position Error
Limit |
|
Yes - Error between
command and actual position exceeds user-defined limit. |
Torque Limit |
|
Yes – Torque limit has been exceeded. |
HW Neg. limit |
|
Yes - Hardware negative limit
activated. |
HW Pos. limit |
|
Yes - Hardware positive limit
activated. |
SW Neg. limit |
|
Yes - Software
negative limit exceeded. |
SW Pos. limit |
|
Yes - Software positive limit
exceeded. |
Feedback Fault |
|
Yes - Feedback fault detected. |
Amp Warning |
|
Yes - Amp warning. |
Motion Done |
|
Yes - Move command completed. |
At Velocity |
|
Yes - Commanded velocity attained. |
Out of Frames |
|
Yes - Out of Frames. A Motion Done event was generated from a Motion Supervisor object. See MPIEventType. |
Action Source |
Controller | User |
Controller - Last action was commanded by the controller.
User - Last action was commanded by you.
See MPIActionSource. |
|