XMP Data Architecture
This section provides a dynamic look at the XMP's data
architecture, between board components, and between the controller and
external devices such as drive amplifiers.
XMP Power-up Sequence
When first powering-up the XMP controller, several actions
initialize the controller according to the firmware's settings and prepare
it for motion control.
Power is Applied
During power-up, the host computer initializes. Power is also supplied
via bus lines to the XMP controller and other devices connected to the
PCI bus. The XMP controller's power supervisor waits for the bussed power
supply to attain voltage thresholds (2.93 for 3.3 VDC power, and 4.63
for 5 VDC power) before powering the controller's components. Until power
fully stabilizes, the board is kept in a reset condition.
Once initialized, the CPU bios polls the bus and assigns
an address to each device (including the XMP controller).
PCI handshakes with SHARC DSP
and Lattice
When the XMP controller's PCI receives a bus address from the host computer's
CPU bios, it handshakes with the SHARC and Lattice.
FPGAs Loaded
With the FPGA's file format determined, the SHARC loads both FPGAs with
the following:
|
- DSP variables (including default timing
parameters)
- FPGA image
- SIM4 FPGA image (if a SIM4 module
is installed)
|
Firmware loaded from flash
memory into the DSP
With the FPGAs loaded, the controller is now ready to load the firmware
from flash memory to the DSP.
DACs calibrated and activated
At the beginning of the power-up process, the digital-to-analog converters
(DACs) are kept grounded (i.e., in an inactive, OFF state) until the controller
is ready to switch them in. This avoids erroneous inputs-outputs with
the drive. After the DSP is loaded, the DACs are internally calibrated
and activated. The system may now accept input from the drives and send
commands.
|
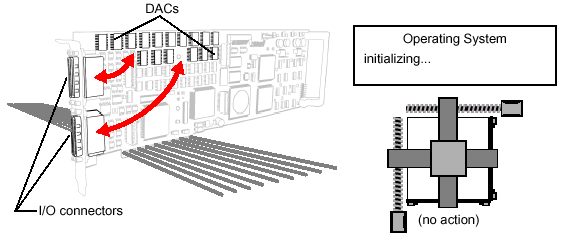
|
Controller Initializes
The controller's boot configuration is based upon parameters stored in
flash memory; these determine the controller's (and drive's) start-up
behavior. One of the programmer's first tasks is to define what this "hello
world" starting state ought to be immediately after power-up. In some
instances, it may prove advantageous to keep a default boot configuration
in flash memory, then modify it from the application during boot-up. In
other instances, it may be better for the application to flash the controller's
memory with an entirely new set of parameters during boot-up. The user
must determine the best approach.
Controller configuration can be done using Motion Console;
however, during development of an application, it is the programmer's
responsibility to write code that properly configures the controller for
its next session upon exit of the application. The controller should utilize
safe amp enabling and hardware I/O to prevent runaway conditions during
start-up.
For this example, we will assume the following safety
measures:
|
- The drive is configured for active
high amp enabling. (That is, the drive cannot be enabled without
controller input.)
- The controller is configured to awaken
with the Amp Enable line set to low (off). This should keep an
active high drive disabled.
- The controller is configured to trigger
an Abort if the Position Error is greater than some specified
value. Because the controller's data registers are all set to
zero at start-up (including the Command and Actual Position values),
any mechanical movement will produce a Position Error. By triggering
an Abort based on Position Error, the controller safeguards against
uncommanded moves.1
|
Device Driver and Operating
System Loads
At this point, the XMP controller is initialized and ready for use. The
next and final phase of the power-up sequence is the loading of the XMP's
device driver and operating system on the host computer. This must be
completed before any motion control application can be loaded and run.
The XMP controller's device driver is shipped to load
manually; however, it can be reconfigured to load automatically. To view
the XMP's device driver, access your operating system's Devices window.
(In WindowsNT? environments, the XMP controller's device driver is labeled
as MeiXMP.)
The operating system completes its loading within several
seconds of the XMP's initialization.
Load Motion Control Application
Application boot-up
When a motion control application (e.g., Motion Console) is loaded, it
first verifies that the XMP controller is operational. The user interface
is displayed and is now available for use.
Create Control Object and Initialize Controller
Before any motion application can move axes, it must
create a controller object and initialize communication. This is a standard
requirement for any application which intends movement.
Homing the Motion Control System
Homing is the setting of a coordinate system through
detection of a known point in space (the "home" point). A home point can
be defined using a limit switch, or by detecting a signal from the encoder
such as a home or index pulse. This is typically the first act a controller
must perform before running the main application code.
Before homing, objects must be created and the controller
must be initialized (see above). One example of a homing sequence is shown
below, consisting of:
|
- Configure a capture to trigger
off the home input.
- Configure a home event action.
- Arm the capture.
- Command a velocity move while
polling the capture trigger.
- When the trigger changes (at
the home point), set the origin.
- Move the axis to the origin.
|
This homing example is taken from the home1.c sample
application program, which may be found in the Sample Applications module
and should be studied. For sake of clarity, excerpts are included below.
Configure the Capture trigger
After the motion objects are created and the controller is initialized,
the MPI must configure and arm a capture. The trigger in this example
is a home sensor (limit switch) on a stage.
Define motion parameters In preparation for commanding
moves, there are several motion parameters which must be defined:
Two types of moves are used for this sample homing routine:
a velocity move and a trapezoidal move. The velocity move consists simply
of running the axis at a set velocity, hunting for the home point, without
regard to its starting and ending positions.
Because a trapezoidal move requires beginning and ending
positions (and we don't know the axis coordinates until the home point
is detected), the first move must be a velocity move. After coordinates
are established through detection of a home point, a trapezoidal move
may be used to move the axis to the origin.
Configure the home event action
The "home event" is the what we use to detect the home point. The home
event could be an input from a limit switch, triggered when the axis runs
into it. The home event could be a home or index pulse on the encoder.
For this example, the stage's HOME switch is used as the trigger, and
the trigger's input is configured to be TRUE (active edge).
The "home action" is what happens when the home is detected.
In this example, the programmer has decided to define the action as a
command to STOP the axis.
Arm the Trigger
With the home event and action defined, all that is left is to "arm" the
trigger by setting the mpiCaptureArm to TRUE. Recall that earlier, this
was set to FALSE to "disarm" the system.
Start a Velocity Move
With the capture event and action defined, and the trigger armed, we are
ready to hunt for the home point. This is accomplished by commanding a
velocity move. Before the axis can be commanded, however, the XMP controller
must first enable the drive. In this example, it is assumed that the drive
is wired to be an active high type; therefore, the Amp Enable line is
set to high (on). Drive enabling via software must be done as a separate
code item and is not shown here:
As the leadscrew rotates, the slide approaches the home
sensor.
Poll Trigger Status
With the trigger armed, the software's next task is to poll the status
of the trigger while the axis continues rotating.
Home Event Detected
As the axis motor continues turning, the leadscrew rotates until the stage
makes contact with the home sensor; this acts as the trigger. When the
trigger event is detected, the encoder position is captured and a stop
action is initiated.
Define the home position as
the origin
When the home pulse is detected in our example, another simultaneous action
is initiated: the axis's position is captured by the FPGA. At this point,
the axis position is recorded in memory. Meanwhile, the axis slows to
a stop. The mpiAxisOriginSet command is then used to set the capture position
to zero, making it the new origin of the axis's coordinate system.
Move axis to the (new) origin
Our sample homing routine's last task is to move the axis to the origin.
Recall that the home pulse was detected while in motion, and that after
detection, the axis coasted to a stop. This means that the axis is now
somewhere beyond the home point (our new origin).
Because we now have a coordinate system, we can perform
a backward trapezoidal move from the current position to the intended
position (the origin).
Delete Objects
Finally, the homing routine must delete the objects it has created. This
is performed with a number of deletion objects such as mpiMotionDelete,
mpiAxisDelete, mpiMotorDelete, etc.
Internal Data Movement via
"Riptide"
Within a typical SHARC timer cycle, data is moved back and forth between
the SHARC and the FPGAs and various feedback devices (e.g., encoders,
resolvers, etc.). On the XMP controller, this is performed over a proprietary,
dedicated data bus called the "Riptide." The Riptide is the serial backbone
of all motion data flow. Within a given SHARC cycle, data moves first
from the SHARC to the FPGAs, and then to the drives. Within the same cycle,
data is moved in the opposite direction (inbound) from the drive and encoder(s)
to the SHARC.
As more drives and encoders are added to the motion
control system, the required data bandwidth increases across the Riptide,
occupying a greater portion of the foreground tasks.
1. IMPORTANT! Use of Position Error
and other positional inputs as safeguards assumes: a) good data connection
between the encoder(s) and controller; b) normal conditions. If a higher
level of safety is required, then extra measures should be utilized, such
as broken encoder wire detection.
|